Refined Linseed Oil
Highest quality Dutch linseed oil used as a medium for oil colours. Increases gloss and transparency.
Adds a soft, ‘slippery’ quality when added to oil colours.
Made by crushing steam heated flax seed to produce greater quantities of oil than in cold pressing. Treated with alkalis post-pressing and water washed to remove the precipitated salts.
Constituents
Linseed Oil. Extracted from Flax seed (Linum Usitatissimum) using steam-heated pressing method. Alkali treated.
Product code:
002
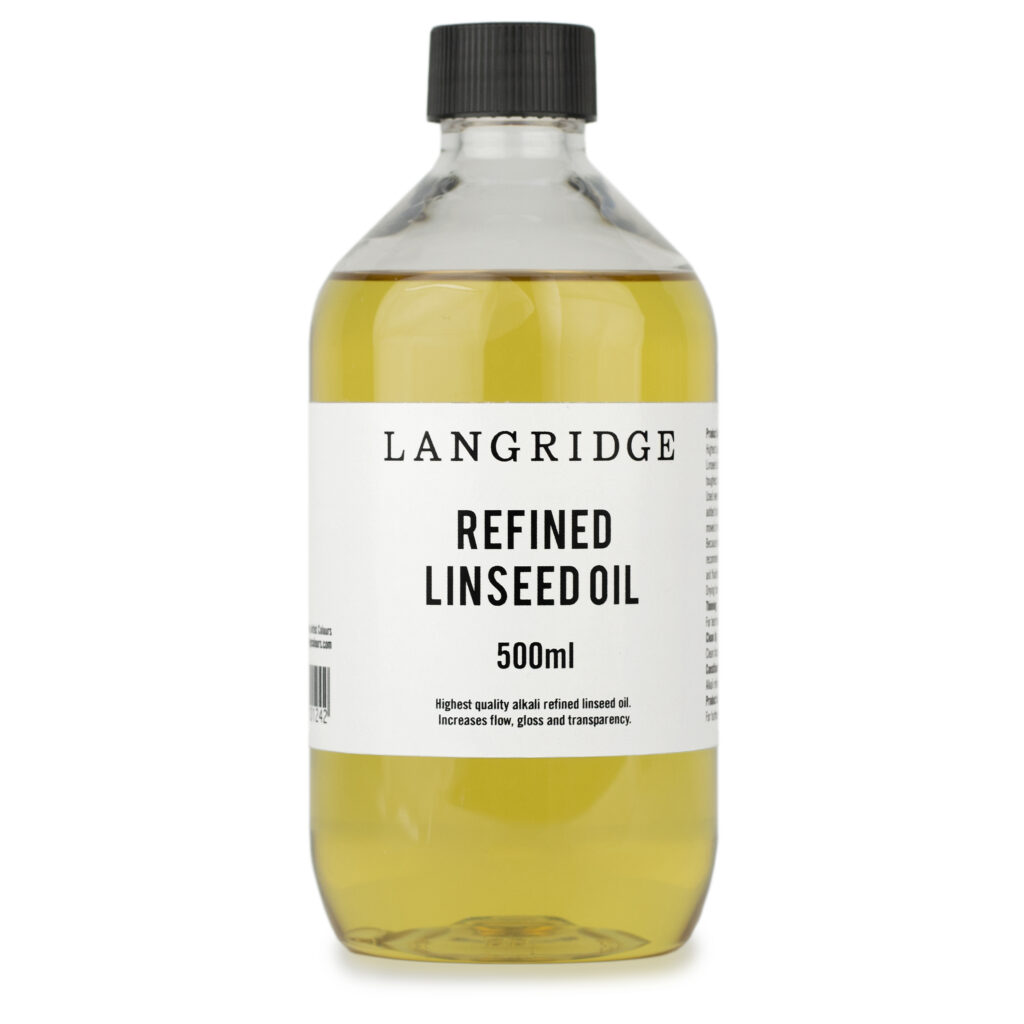
Refined Linseed Oil Product Information
Product Application
Langridge Refined Linseed Oil may be used for the grinding of oil colours. It may also be added to oil colours and oil mediums at the discretion of the artist.
Alkali refined linseed oil is the most frequently employed oil for manufacturing artists’ oil colours. It does not have as great a wetting power as cold pressed linseed oil however it’s refinement process makes it less prone to yellowing over time. For more information on the grinding of oil colours.
Refined Linseed Oil adds a loose, slippery quality when added to oil colours and mediums. It is recommended however, that the use of linseed oil, whether cold pressed or refined, should be used sparingly to extend oil colours as it is prone to yellowing more than other oils. If wishing to employ glazes or washes Langridge recommends the use of Stand Oil, a virtually non-yellowing oil as the basis for painting mediums.
The paint film will stay open and is easily moved or reworked for up to 24 hours.
Langridge Refined Linseed Oil should be considered a ‘fat’ medium. It should not to be excessively used in underpainting if oil colours with no additional medium are to be applied on top.
Dries to a gloss finish.
The Drying of linseed oil films
Linseed oil is the most widely used oil because when dry it forms the toughest, most resilient paint films.
Linseed, like all artists’ drying oils, harden by absorbing oxygen. As it oxidises, it also polymerizes at a molecular level being changed into a non-reversible film. Alkali refined linseed oil due to it’s low acid content has less tendency to yellow.
Problems with ambient temperature and humidity
Because artists drying oils (oils that dry to a hard, non-reversible film) absorb oxygen to harden, so the ambient temperature and humidity have an effect on the speed and success of film hardening.
Oils, oil paints and oil mediums should not be applied in temperatures below 10° C or above 40° C.
Relative humidity level should not exceed 50%. Moisture in a high humidity environment will create a fine layer of water on top of the paint film preventing oxygen from being absorbed. This will dramatically slow the hardening of the oil, potentially weakening the paint film even when fully dry.
Temperature and relative humidity can be controlled in the artists studio with heating/cooling devices and the use of dehumidifying devices.
Apparent darkening of oil paintings kept in dark storage
When a painting has been stored for a period of time in darkness the artwork will darken. This can be reversed by re-exposure to sunlight. Exposure to sunlight will not reverse the long term effects of oil paint films darkening. Reversal of darkening takes between 3 months and a year depending on type of light exposure (natural, fluorescent, indirect). Do not over-expose artwork to excessive light for long periods of time as non-lightfast colours may fade.
Thinning
For best results thin with Distilled Gum Turpentine. However, Langridge Low Toxic Solvent Solvent or Solvent 75 may be substituted. Due to the lower solvency action of the latter solvents, an increase in ratio compared to turpentine may be required. Over-thinning with solvents can lead to the partial destruction of the paint film. Langridge recommends a dilution rate of no more than 30%.
Appearance
Langridge Refined Linseed Oil is a pale yellow colour liquid with characteristic linseed odour.
The colour of the oil will slightly effect the oil colours with which it is mixed.
Clean Up
Clean brushes with any artists’ solvent (eg Gum Turpentine, Low Toxic Solvent, etc.).
For further washing apply a small quantity of Marseille or other pure olive oil soap and massage the bristles of the brush to release any remaining colour. Wash thoroughly in warm water. Leave to fully dry before using for oil colours.
Drying Times
12-24 hours to touch dry.
Full film drying 3-6 months